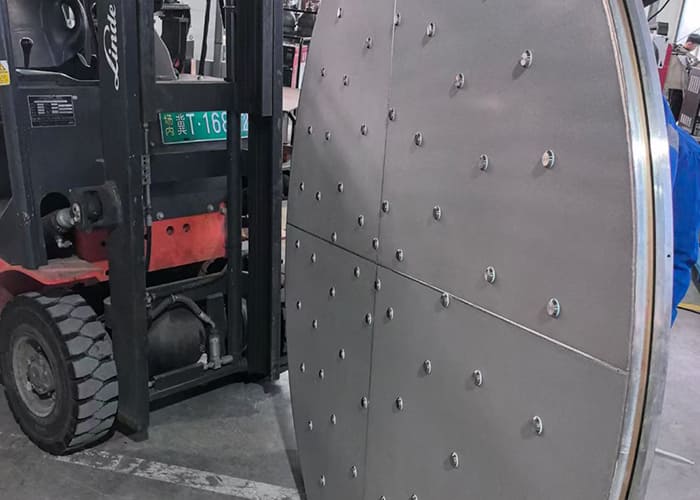
Overview
Client
Confidential
Timeline
Eight (8) working weeks
Sector
Industrial manufacturing
Project
Replacement of Micro-Perforated Fluidisation Panels with SintAbond™ MESH
Product specified
CFL SintAbond™ MESH 316 Stainless Steel
Objective
Improve durability and gas flow efficiency
Result
Increased productivity, reduced consumption of gas with lower operating costs
Background
The client, a pharmaceutical manufacturing company, faced significant challenges with their existing fluid bed dryer performance. The fluidisation panels, crucial for ensuring gas flow distribution and maintaining process efficiency, were underperforming and prone to damage. This inefficiency and vulnerability led to frequent downtime and complex replacement procedures, adversely impacting operational performance and increased maintenance costs.
To address these issues, the client sought a more durable and efficient alternative that could withstand the rigors of their process, whilst providing the necessary porosity and differential pressure, necessary for effective fluidisation.
Objectives
Durability
Replace easily damaged micro-perforated panels with a more robust solution.
Efficiency
Improve porosity and differential pressure, to provide effective air distribution.
Reduced downtime
Minimise downtime associated with panel damage and replacement.
Energy efficiency
Enhance gas distribution, potentialy reducing consumption.
Solution Provided by CFL
CFL specified a material from their series of SintAbond™ MESH, a sintered multi-layered mesh, manufactured in 316SS. This solution offered the following advantages:
Enhanced durability
The sintered mesh construction provided a harder-wearing alternative to the micro-perforated panels, significantly reducing susceptibility to damage.
High porosity
The design ensured the high porosity necessary for effective fluidisation, maintaining process efficiency.
Improved gas flow
The SintAbond™ MESH structure facilitated increased gas flow, enhancing distribution, optimising process effeciency.
Implementation
1. Needs assessment
CFL collaborated with the client to understand their operational challenges and specific requirements for fluidisation. This included analysing the limitations of the existing micro-perforated panels and identifying opportunities for improvement.
2. Product specification
Based on the assessment, CFL specified the optimum SintAbond™ MESH product for the application. The material specified offers excellent mechanical properties, corrosion resistance, and suitability for high-performance applications. The design focused on optimising the mesh structure to balance durability with the required porosity and differential pressure, to provide effective fluidisation.
3. Installation and testing
CFL provided technical support for the installation of the SintAbond™ MESH panels, ensuring a smooth transition from the original micro-perforated panels. Initial testing demonstrated a much improved gas distribution and the potential to reduce gas flow by approximately 10% due to the increased efficiency of the design.
Results
Increased durability
The robust construction of the SintAbond™ MESH panels dramatically reduced the frequency of damage, minimising downtime, and associated maintenance.
Enhanced productivity
The durability and improved gas flow reduced operational downtime, contributing to increased productivity.
Reduced gas consumption
Enhanced gas distribution efficiency contributed to a reduction in gas usage by an estimated 10%.
Lower operating costs
The reduction in gas consumption and maintenance needs contributed to significant cost savings for the client.
Future Applications
Encouraged by the performance of the CFL SintAbond™ MESH, the client has requested similar replacements for other equipment on site. This further emphasises the success and potential of the CFL solution in enhancing processes efficiencies across various applications.
Conclusion
The implementation of CFL SintAbond™ MESH provided the client with a highly durable and efficient solution. The robust design and improved gas distribution resolved the issues associated with the original micro-perforated panels, significantly reducing operational costs.
By delivering a customised high performance product, CFL demonstrated its capability to innovate and provide effective solutions that address specific industrial challenges.
Key Takeaways
Innovative design
The SintAbond™ MESH panels offer a superior alternative to micro-perforated panels, enhancing both durability and efficiency.
Operational efficiency
Improved gas distribution and reduced downtime contributed to higher productivity and energy savings.
Client expansion
Success with initial implementation has led to further opportunities for CFL to provide solutions for additional equipment within the client’s operations.
Client Feedback
“From an operational perspective, the SintAbond™ MESH panels work a dream. Initial tests indicate we can reduce the gas flow by around 10% as distribution is much improved.”