Engineered solutions: Maximising Filter Vessel Productivity and Efficiency
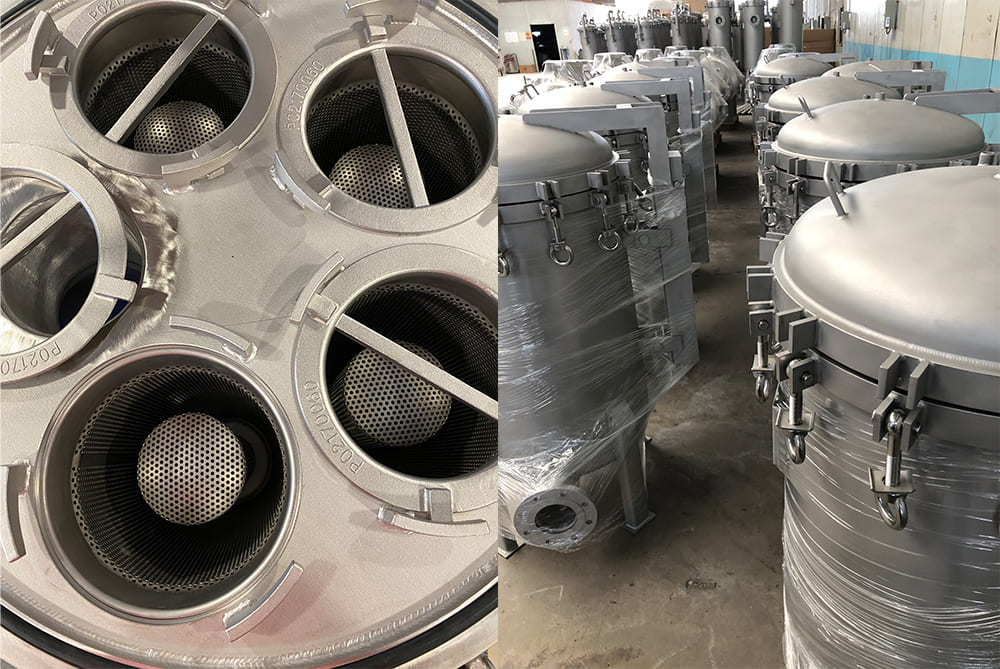
Engineered solutions: Maximising Filter Vessel Productivity and Efficiency
Challenges Impacting Filter Vessel Productivity:
1. Increased Production Demands
2. High Maintenance Costs
3. Ageing Infrastructure
4. Inadequate Maintenance
5. Limited Flexibility
Old equipment often lacks the flexibility to accommodate different types of filter internals or adapt to varying process conditions. This rigidity can limit effectiveness in meeting current filtration and separation demands, ultimately impacting productivity.
Engineered Solutions for Enhanced Efficiency
1. Optimising Flow Dynamics
The internal design of a filter vessel profoundly impacts fluid flow. By performing Computational Fluid Dynamics (CFD) analysis, engineers can simulate flow patterns and identify areas of turbulence, stagnation, or uneven distribution. Based on CFD results, several modifications and retrofitting can be implemented:
- Optimising internal baffles, diffusers, and distributors can strategically redirect fluid flow, minimising turbulence and ensuring uniform distribution across filter internals and filter media. This promotes even loading of filter internals and media, maximising utilisation and improving filtration efficiency. Baffles help to break up large eddies and create more laminar flow, while diffusers and distributors help to spread the flow evenly.
- Integrating flow straighteners can reduce turbulence and promote laminar flow. By minimising swirling and chaotic flow patterns, flow straighteners improve the efficiency of the filtration process and minimise pressure drop.
2. Upgrading Filter and Retrofitting Internals
Advances in filter media technology offer opportunities to improve throughput, filtration efficiency, solids loading capacity, and filter service life.
Upgrading existing filter internals through retrofitting can significantly enhance performance. This approach addresses bottlenecks of poorly performing and undersized equipment, improving contaminant removal, reducing pressure drop, and extending filter service life. Often, retrofitting can be undertaken without the need for any vessel modifications.
CFL’s engineering expertise enables seamless integration and retrofitting of critical process internals, optimising existing equipment to adapt to accommodate process changes or debottlenecking requirements.
3. Material Upgrades and Coatings
The materials used in the construction of the vessels and housings can significantly impact its performance and longevity.
Upgrading to corrosion-resistant alloys or applying protective coatings can significantly enhance the longevity of the equipment, reduce maintenance costs, and improve safety. This is particularly important in harsh chemical environments.
Replacing failing and incompatible seals with high-performance elastomers can prevent bypass and maintain filtrate quality. This ensures that the filtration process is effective and prevents contamination of the downstream process.
4. Enhancing Cleanability and Maintainability
Efficient maintenance is essential for maximising the productivity and service life of a filtration system. Implementing quick-change filter element mechanisms minimises downtime during replacements, reducing labour costs and maximising production uptime.
Retrofitting vessel internals for easier access to filter elements simplifies maintenance, enabling quicker filter changes, inspections and removal of internal filter components. This reduces the time and effort required for routine servicing.
Integrating automated Clean-in-Place (CIP) systems further enhances efficiency by reducing manual labour, ensuring consistent cleaning performance, and minimising downtime.
5. Integrating Automation and Control systems
Automating control systems can greatly improve the effectiveness and dependability of the filtration process.
Installing pressure sensors and control systems can optimise the filtration process, prevent pressure-related issues, and ensure safe operation.
Implementing flow rate monitoring and control systems can ensure consistent performance, optimise throughput, and prevent overloading of filter internals.
Integrating remote monitoring capabilities allows operators to track system performance, identify potential issues, and schedule maintenance proactively, minimising downtime and maximising efficiency.
6. Vessel Modifications and Debottlenecking
In some cases, more extensive modifications to the vessel itself may be necessary to address bottlenecks and improve performance. If space permits, increasing the vessel size can accommodate more filter elements and increase flow capacity, addressing limitations caused by increased production demands.
Installing multiple vessels in parallel can increase overall system capacity and provide redundancy, ensuring continuous operation even during maintenance or filter changes.
Optimising the piping system connected to the vessel can reduce pressure drop and improve flow efficiency, maximising the overall performance of the filtration system.
Advantages of CFL's Engineered Solutions
Our unique approach combines our engineering expertise with high-quality, in-house manufacturing of equipment and process internals. This synergy delivers several key benefits:
- Custom Design Solutions: We don’t offer a one-size-fits-all approach. Each individual system is designed and manufactured to meet your specific requirements.
- Ongoing Engineering Support and Service: We provide continuous engineering support and service to ensure that the engineered solution continues to perform optimally throughout its lifecycle.
- Long-Term Reliability: High-quality materials and manufacturing processes ensure long-term reliability and performance.
- Reduced Downtime: Our engineered solutions are designed with optimal flow dynamics and precise component selection minimises the risk of clogging and filter element failure, leading to less downtime for maintenance.
Conclusion
While standard filter vessels and housings may be adequate for some applications, many industries require customised engineered solutions in order to meet specific processes.
Our focus on engineered solutions goes beyond simply providing equipment, specialist filter components and process internals; we offer a unique blend of engineering expertise and manufacturing excellence.
By choosing CFL, you’re not just buying equipment but investing in a comprehensive filtration and separation solution designed to meet your specific needs, optimise performance, and deliver long-term value. Contact us today to discuss your filtration and separation challenges and learn how our engineered solutions can enhance your operations.
Make a Comment Cancel reply
Latest News
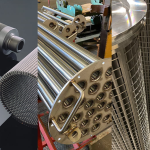
How CFL’s specialised internals optimise filtration process performance
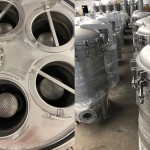
Engineered solutions: Maximising Filter Vessel Productivity and Efficiency
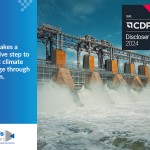
Carbis Filtration achieves grade B in 2024 CDP Disclosure in climate benchmarking

Advantages of sintered metallic filter elements over ceramic filter elements for syngas treatment
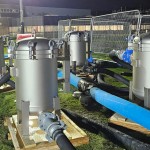
Process equipment rental services: How to choose the correct filtration and separation equipment for your application
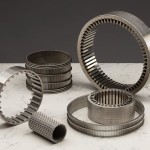
No comments yet.