How CFL’s specialised internals optimise filtration process performance
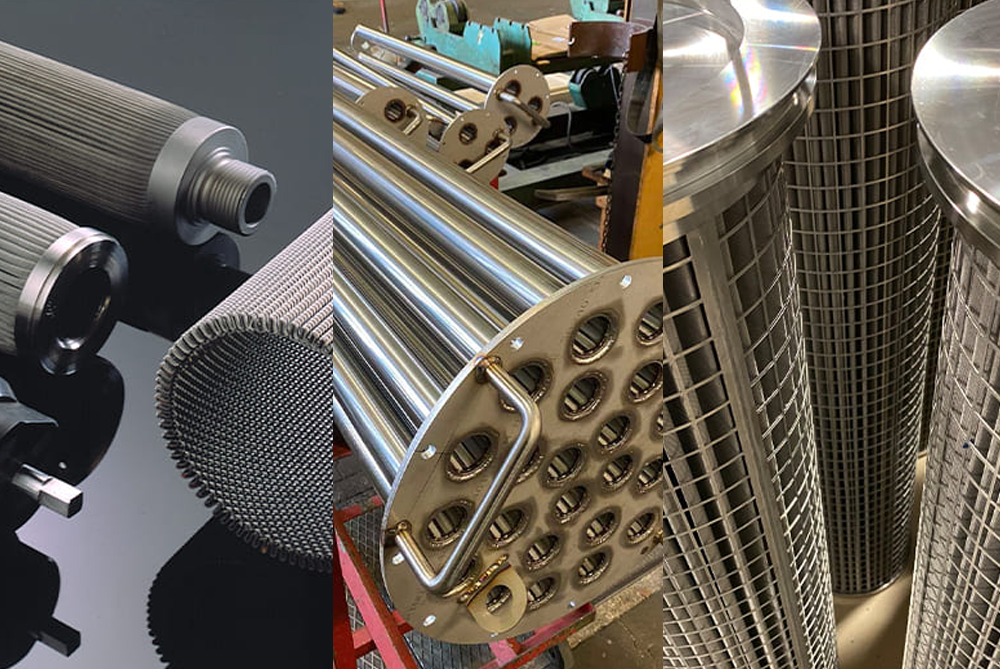
How CFL’s specialised internals optimise filtration process performance
Specialised internals engineered for optimised filtration
CFL’s filter elements are built with precision and engineered for superior performance. Their designs maximise filtration efficiency, reduce pressure drops, and effectively remove contaminants.
1. Precision-engineered pleating for increased surface area and flow dynamics
CFL employs advanced pleating techniques to maximise the surface area of the filter media. This amplified surface area directly translates to an increased dirt-holding capacity, facilitating extended filtration cycles and reduced downtime.
The controlled pleat geometry optimises flow dynamics, minimising channelling and ensuring uniform flow distribution, which is critical for maintaining consistent filtration performance.
CFL’s pleated candle filters, maximise the amount of filtration media within a given volume, which enhances the filtration capacity and reduces the frequency of filter changes.
2. Optimised pore size distribution for targeted particle retention
CFL’s specialised internals feature filter media with carefully regulated pore sizes, ensuring precise particle removal. This enables the targeted removal of particles across a broad spectrum of sizes, ensuring consistent filtrate quality.
The accurate control of pore size distribution is critical for achieving the desired filtration efficiency and preventing premature clogging.
When filtering sensitive chemical solutions, a very precise pore size is required to prevent unwanted particles from passing through and to maintain the chemical integrity of the solution.
3. Reinforced support structures for media integrity under high differential pressure
CFL’s filter elements incorporate reinforced support structures that maintain the structural integrity of the filter media under high differential pressures.
These support structures prevent media deformation and ensure consistent filtration performance throughout the operational lifespan of the element.
CFL’s strainers, for example, are built with strong internal supports to prevent deformation under high pressure, maintaining the integrity of the filtration process.
4. Customised designs for application-specific optimisation
By understanding the unique demands of each filtration application, CFL offers customised designs to meet specific requirements.
The filter media, pleat shape, and internal supports are modified to maximise efficiency for the exact fluids and operational demands of each application.
For example, CFL can design a custom filter candle with specific dimensions, materials, and filtration ratings to fit a pre-existing housing and to meet a unique filtration goal.
How do CFL’s internals optimise filtration through debottlenecking and retrofitting?
CFL’s specialised internals play a pivotal role in debottlenecking, retrofitting, and optimising existing filtration systems, driving operational excellence.
1. Debottlenecking for increased throughput
CFL’s engineered filters remove flow restrictions in existing systems. By increasing dirt-holding capacity and reducing pressure drops, our solutions boost throughput without requiring larger equipment.
This eliminates production bottlenecks, extends service cycles, and maintains optimal flow rates. It helps facilities achieve higher output from their current filtration infrastructure while reducing energy consumption and maintenance downtime.
2. Retrofitting for seamless system upgrades
Our precision-designed filters seamlessly replace outdated elements in existing housings. CFL’s retrofit solutions match OEM dimensions while delivering superior performance through advanced materials and construction.
This cost-effective upgrade path improves filtration efficiency without capital-intensive system replacements. It minimises downtime and maximises the value of current equipment investments.
3. Optimisation for peak efficiency
CFL customises filtration solutions to each application’s specific requirements. Through precise pore sizing, material selection, and flow engineering, we optimise particle retention, energy efficiency, and service life.
Our data-driven approach ensures that filters perform at peak efficiency under exact operating conditions. It reduces the total cost of ownership while maintaining consistent product quality.
Addressing complex filtration challenges with expertise
The industrial sector presents many filtration challenges, from handling corrosive fluids to removing particulates from high-viscosity liquids. CFL addresses these challenges with expertise and customised solutions.
1. High temperature and pressure applications
In industries like petrochemical and chemical processing, filtration systems must withstand extreme temperatures and pressures. CFL’s metallic filter elements are designed to meet these demanding requirements, ensuring reliable performance in harsh environments.
For example, in high-temperature gas filtration within a steel plant, CFL’s high-temperature rated filter candles ensure particle removal while maintaining the system’s integrity.
2. Corrosive fluid handling
Handling corrosive fluids requires filtration systems that can withstand chemical attack. CFL’s use of corrosion-resistant alloys ensures that their filter elements maintain their integrity and performance in corrosive environments.
In a plant processing acids, the corrosion-resistant strainers from CFL prevent degradation and maintain flow.
3. High viscosity filtration
Filtering high-viscosity liquids presents unique challenges, requiring optimised pleat configurations and pore size distributions. CFL’s engineered solutions facilitate efficient filtration of these challenging fluids.
For example, when filtering viscous polymers, CFL’s optimised pleating techniques provide the required flow.
4. Particle retention
To achieve high-purity filtration, CFL employs filter media with rigorously controlled pore size distributions. This level of precision is essential for applications such as pharmaceutical production, where stringent particle retention requirements must be met to ensure product efficacy and safety.
Why Choose Carbis Filtration (CFL)?
Choosing CFL for optimised filtration delivers significant benefits:
- Enhanced efficiency – Specialised internals maximise filtration performance, leading to higher throughput and reduced downtime.
- Improved filtrate quality – Precise pore size distribution ensures consistent and high-quality filtrate.
- Extended operational lifespan – Robust construction and corrosion-resistant materials extend the lifespan of filter elements.
- Reduced operational costs – Optimised filtration minimises energy consumption and reduces the frequency of filter element replacements.
- Customised solutions – CFL leverages its deep understanding and ability to create bespoke solutions to provide filtration systems that precisely meet unique application demands
- Strong reputation – The company website shows a focus on delivering high-quality solutions, implying a strong customer focus and expertise.
Final thoughts
Make a Comment Cancel reply
Latest News
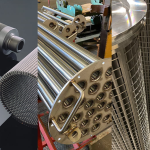
How CFL’s specialised internals optimise filtration process performance
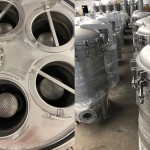
Engineered solutions: Maximising Filter Vessel Productivity and Efficiency
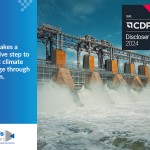
Carbis Filtration achieves grade B in 2024 CDP Disclosure in climate benchmarking

Advantages of sintered metallic filter elements over ceramic filter elements for syngas treatment
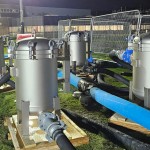
Process equipment rental services: How to choose the correct filtration and separation equipment for your application
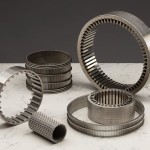
No comments yet.