Process equipment rental services: How to choose the correct filtration and separation equipment for your application
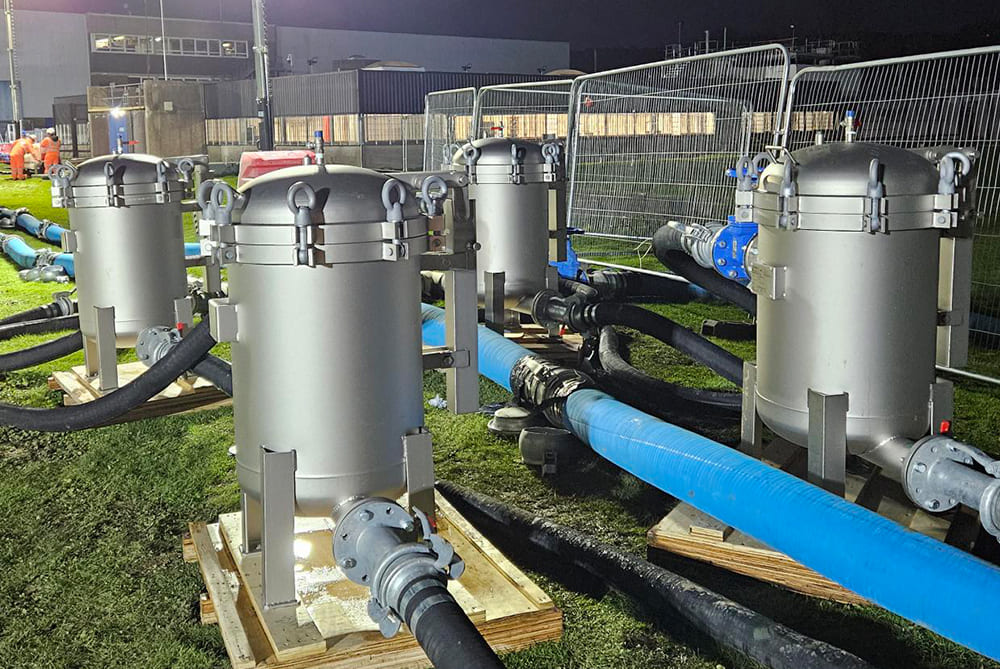
Process equipment rental services: How to choose the correct filtration and separation equipment for your application
Efficient filtration and separation play a crucial role in industrial processes, ensuring the efficient removal of contaminants and unwanted particulates, or the recovery of valuable product, resulting in a final product that meets desired quality specifications. With the growing popularity in equipment rental, businesses can benefit from greater flexibility, cost savings and access to technical expertise and service support. However, selecting the correct equipment is essential for achieving optimal performance and project success.
Factors to consider when selecting rental process equipment
Selecting the correct filtration and separation equipment requires a clear understanding of specific process requirements. The key factors to consider include.
1. Specific application analysis
Type of liquid solution
Identify the liquid to be filtered — water, wastewater, fuel, chemicals, or food products; each presents its own set of unique challenges. Factors such as temperature, pressure, viscosity, corrosivity, play a crucial role in selecting the appropriate filtration and separation technique. Understanding these characteristics ensures optimal performance and efficiency.
Particle size and distribution
Analysing the size, distribution, and concentration of the particulates to be removed is essential. This data directly determines the required pore size of the filtration media and influences the equipment overall capacity. Accurate particle characterisation ensures efficient filtration and separation, minimises premature fouling, extending service life of the filter media.
Desired flow rate
What is the throughput of the process? Understanding the required flow rate is essential to ensure the equipment can handle the volume of liquid required within the specified timeframe.
Solid-liquid separation efficiency
Determine the required level of solids removal efficiency based on process specifications and regulatory standards. Evaluating the desired separation level is crucial, particularly when ensuring compatibility with downstream processes and maintaining compliance with industry regulations. This assessment helps select the most suitable filtration technology for optimal performance.
Safety
Identify potential hazardous materials associated with the process, including corrosive, toxic or flammable substances. Handling such materials may demand specialised equipment engineered for elevated temperature and pressure, chemical resistance and containment to ensure safe operation. Implementing appropriate safety protocols is essential for maintaining regulatory compliance and protecting both personnel and the environment.
2. Selecting the correct equipment
CFL offers various pieces of filtration and separation equipment available for rental, each suited to a particular application. Some of the more common rental options are detailed below:
Strainers and Coarse Filters
These filters are ideal for high flow rates and large particulates and serve as excellent pre-filters for more complex filtration processes.
Bag Filters
A high-performance, cost-effective choice designed for various applications, these filters trap contaminants as liquid flows through replaceable filter bags and are suitable for a wide range of small batch and bulk processing applications.
Cartridge and Candle Filters
Providing customised, high-integrity solutions, these filters are available with metallic cleanable cartridges or disposable polymeric filter cartridges, providing a broad range of filtration efficiency.
For a deeper understanding of these options, consult CFL, a trusted filtration equipment rental company.
3. Key capacity and performance considerations
It is important to select equipment that meets each project’s capacity and performance demands. Here are some capacity and performance-related factors to consider:
Processing capacity
Ensure the equipment can handle the required flow rate and solids loading. Selecting equipment with insufficient capacity can create bottlenecks, reduce operational efficiency and increase maintenance demands. Correct sizing and capacity assessment is essential for maintaining smooth and reliable system performance.
Filtration efficiency
Ascertain equipment capability to achieve the necessary level of particulate removal. This is a critical performance metric in industrial filtration processes, directly affecting product quality, process reliability, and regulatory compliance.
Operational pressure and temperature
Confirm that the equipment operates within the pressure and temperature ranges relevant to your process. Exceeding limitations can result in equipment damage, reduced filtration efficiency, system failure and danger to personnel.
By thoroughly understanding the filtration needs and evaluating suitable equipment options, you can optimise process efficiency, enhance operational performance and achieve desired results, whilst ensuring compliance with industry standards.
4. Regulations and compliance
Adhering to industry specific regulations and compliance standards is crucial when selecting filtration and separation equipment. This ensures safe and efficient operations while minimising environmental impact. In terms of quality and safety, equipment must be selected that meets necessary regulatory compliance.
Why is it important to choose the correct filtration and separation solutions?
When it comes to filtration and separation equipment, choosing the correct solution is essential for a multitude of reasons:
Maximising process efficiency
Selecting the correct filtration technology involves evaluating several key factors to ensure optimal system performance, process efficiency, and product quality. Essential criteria to guide equipment selection includes, process requirements, filtration efficiency, media selection, system operating conditions, contaminant loading, and compliance and safety standards.
By evaluating given criteria, businesses can select equipment that delivers long term reliability, enhanced productivity, and minimise downtime.
Preventing equipment damage and downtime
If equipment is not designed to handle specific process conditions – such as operating pressure, temperature, or chemical compatibility, the risk of costly breakdowns, operational downtime and compromised safety increases significantly. Selecting equipment with the appropriate design considerations ensures system reliability, enhances operational safety, and minimises maintenance and repair costs.
Controlling operational costs
Rental services provide businesses with a cost effective, flexible, and risk-mitigated solution to meet operational demands. Whether for short-term projects, temporary requirements, or testing purposes, renting grants access to specialist process equipment without the financial and logistical burden of ownership. CFL offers both short-term and long-term rental options, delivering customised solutions to align with project timelines and operational goals.
Enhancing safety and environmental responsibility
Inadequate filtration and separation can lead to the release of harmful pollutants into the environment or contamination of the product stream, posing significant safety and environmental risks. Implementing efficient, engineered filtration and separation solutions minimises such risks, supporting regulatory compliance and reducing environmental impact.
Benefits of partnering with a reliable rental provider
Navigating the selection of the correct equipment can be a daunting task, but a knowledgeable rental provider can make the process much smoother:
Expert equipment selection
Rental companies with extensive expertise in filtration and separation applications can guide you in selecting the most suitable equipment for your specific needs. Expert knowledge ensures that the equipment is not only suitable but also optimised for the desired flow rates, pressure conditions, and temperature tolerances. This leads to better filtration efficiency, reduced energy consumption, and minimised operational disruptions. Adjusting operating conditions based on expert recommendations can extend the life of the filtration media and improve throughput.
Mastering operation and performance
They can share technical expertise to help you operate the equipment efficiently and achieve peak performance.
Technical support
A reputed rental company should provide access to a dedicated team of engineers ready to address any questions or concerns that may arise during the rental period.
Why choose Carbis Filtration Limited?
Carbis Filtration Ltd (CFL) stands out as a trusted provider of specialist process equipment:
Extensive equipment inventory
CFL offers an extensive range of engineered filtration and separation solutions, featuring a diverse selection of process equipment. We provide businesses with access to the right solutions for a wide variety of applications, ensuring that each process is supported with the most suitable equipment for optimal performance, efficiency and reliability.
Technical expertise
With a team of seasoned experts, we offer guidance and support, ensuring you select the ideal equipment and operate it to its fullest potential.
Comprehensive turnkey solutions
CFL offers more than just rental equipment; we offer complete rental solutions including equipment installation, operational support, and on-site technical assistance. This ensures you all the necessary resources for effective filtration and separation.
Commitment to customer satisfaction
Our expert team is dedicated to helping clients achieve their filtration and separation goals with the right rental equipment.
Application support
We offer consultation and technical guidance to help clients select the most appropriate equipment for the application.
Project management support
With years of extensive experience across a wide range of applications, CFL can assist with project planning, logistics, and on-site operational support if needed.
Focus on safety and reliability
CFL is committed to providing well-maintained equipment and prioritising safety considerations.
Conclusion
Choosing the right rental filtration equipment requires careful consideration of several factors, including the specific application needs, desired performance, and regulatory compliance. Working with a reputed and experienced rental provider like Carbis Filtration Limited allows you to select the most suitable equipment that meets your unique needs.
If you have any questions or require further assistance in selecting the correct equipment for your application, don’t hesitate to contact our experts. Our technical team is ready to discuss your specific filtration and separation requirements, and recommend the most appropriate equipment for your project.
Latest News
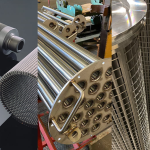
How CFL’s specialised internals optimise filtration process performance
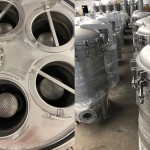
Engineered solutions: Maximising Filter Vessel Productivity and Efficiency
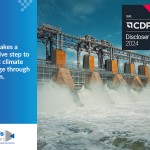
Carbis Filtration achieves grade B in 2024 CDP Disclosure in climate benchmarking

Advantages of sintered metallic filter elements over ceramic filter elements for syngas treatment
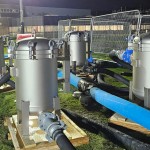
Process equipment rental services: How to choose the correct filtration and separation equipment for your application
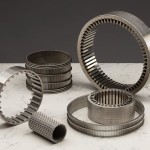
No comments yet.